Pigging Paint Systems: Revolutionizing Efficiency in the Paint and Coatings Industry
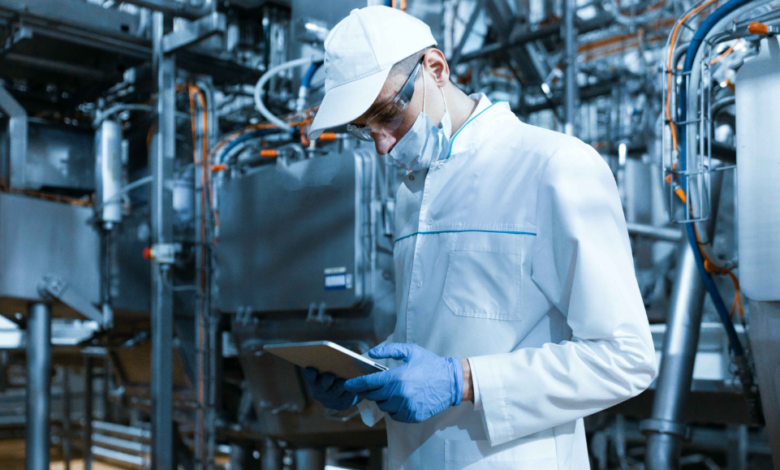
In an industry where color, consistency, and cleanliness are critical, manufacturers are continuously exploring ways to reduce waste and streamline production. One highly effective method that has gained traction in recent years is pigging paint systems. These systems are transforming how paints and coatings are processed by improving product recovery, reducing contamination risk, and minimizing cleaning time.
For companies producing paints, varnishes, resins, and coatings—whether for automotive, decorative, industrial, or protective purposes—pigging systems represent not just an operational upgrade, but a strategic investment.
What Is Pigging in Paint Manufacturing?
In simple terms, pigging involves sending a projectile (known as a “pig”) through a pipeline to push out the product that would otherwise remain trapped inside after each batch. This process recovers product, cleans the line, and prevents waste—all without requiring manual disassembly or extended flushing processes.
In pigging paint operations, this technique becomes especially valuable. Paints are viscous, often solvent-based, and require strict control over color and chemical purity. Residual paint left behind in pipelines between batches not only leads to material loss but also risks cross-contamination when changing colors or formulations.
See also: How AI Face Swap Technology Is Shaping User-Generated Content
Why Pigging Paint Makes Sense for Coating Manufacturers
Pigging systems are not just a technical novelty—they provide real, measurable benefits for paint manufacturers. Here’s why many facilities are implementing pigging paint solutions:
1. High Product Recovery Rates
Paint is a high-value product. Every liter lost due to pipeline residue cuts into profits. With a pigging system in place, manufacturers can recover up to 99.5% of the product left in the pipeline after a batch run. This significantly improves overall yield and reduces the amount of discarded paint.
2. Reduced Waste and Disposal Costs
Paint disposal is tightly regulated. Waste paint must be handled as hazardous material in many countries, requiring special treatment and increasing operational costs. By pigging paint pipelines, companies can reduce leftover paint and thus minimize waste generation and the associated disposal fees.
3. Faster Color Changeovers
In facilities that produce multiple paint colors, switching from one to another requires extensive cleaning to avoid color mixing. Pigging clears the line more effectively than water or solvent flushes alone, dramatically reducing downtime and cleaning material use.
4. Improved Hygiene and Cleanliness
While hygiene might be more associated with food or pharma sectors, cleanliness in pigging paint systems is equally important. Residual materials can harden or chemically react if not removed promptly, damaging the pipeline and affecting the next batch’s quality.
5. Lower Use of Cleaning Solvents
Pigging systems minimize the need for aggressive chemical cleaning. This not only reduces environmental impact but also lowers operational risks related to worker safety and chemical handling.
Components of a Pigging Paint System
To understand how pigging paint solutions work, it’s important to break down their core components:
- Pig: The device pushed through the pipe, often made of silicone or food-grade rubber, and designed to form a tight seal to scrape off and push forward residual paint.
- Pig Launcher and Receiver: These are the entry and exit points of the pig. The launcher inserts the pig into the pipeline, and the receiver collects it at the other end.
- Pig Detection System: Sensors are used to track the pig’s location in real-time, ensuring it moves correctly through the system and completes its path.
- Propulsion Source: This could be air, nitrogen, or another fluid used to push the pig through the line.
These components must be selected and installed carefully to suit the specific needs of paint manufacturing, including the type of paint, pipeline diameter, and level of automation required.
Key Considerations When Implementing Pigging Paint Systems
Every paint production facility is different. While the benefits of pigging paint are well established, several factors must be considered for successful implementation:
1. Viscosity and Flow Behavior
Different types of paints—latex, acrylic, solvent-based, or epoxy—have unique viscosities and settling behaviors. A system optimized for water-based paint may not work efficiently with high-viscosity coatings. The pig material and sealing strength must be matched accordingly.
2. Pipeline Configuration
Curved pipes, vertical runs, and branch lines require specific pig designs and careful propulsion planning. Straight-line pipelines allow easier pigging, but most paint plants have complex routing due to their batch nature.
3. Cleaning Requirements
Some pigments or additives leave residues that require specialized cleaning processes. The pigging system should integrate with existing CIP (Clean-in-Place) or solvent-cleaning routines to ensure full sanitation between batches.
4. Color Separation
In decorative and automotive paint facilities, color contamination is a major issue. Pigging provides a clean sweep of the line, preventing even trace amounts of previous colors from affecting the next batch.
Real-World Example: Pigging Paint in Action
A mid-sized decorative paint manufacturer in Europe implemented a fully automated pigging paint system on four of its main color lines. Prior to pigging, each changeover required 120 liters of solvent and 45 minutes of cleaning time. After installation:
- Product recovery increased by 96%
- Solvent usage dropped by 70%
- Changeover time reduced by 40 minutes
- ROI was achieved in under 12 months
This example highlights how the combination of environmental, operational, and economic benefits makes pigging a strategic upgrade.
Conclusion
As the paint and coatings industry evolves, the demand for efficient, cleaner, and more sustainable production is increasing. Pigging paint systems offer a forward-thinking solution that improves product recovery, reduces downtime, and supports responsible manufacturing practices.
For paint manufacturers looking to remain competitive while reducing waste and complying with stricter environmental laws, pigging isn’t just a process—it’s a business advantage. By investing in the right system, tailored to your pipeline and product requirements, you unlock operational efficiency that pays dividends for years to come.