Foam Conversion and Bespoke Acoustics: A Comprehensive Guide
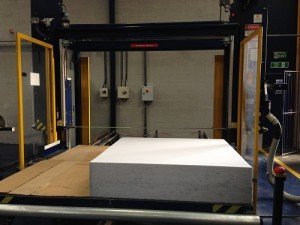
Foam conversion is the process of transforming raw foam materials into specialized products that meet unique industry needs. This involves cutting, moulding, laminating, and fabricating foam into custom solutions, such as bespoke acoustics, insulation, packaging, and medical applications. With advanced technology and precision engineering, foam conversion enables businesses to develop innovative products that offer comfort, protection, and soundproofing.
Understanding the Foam Conversion Process
The foam conversion process includes multiple steps and techniques to achieve the desired product specifications. Here are some of the key processes used in foam conversion:
1. Cutting Techniques
- Band Saw Cutting: Used to cut foam into specific shapes and sizes with precision.
- Profiled Slitting: Enables cutting foam into thin, uniform layers.
- CNC Profiling Machine: Allows intricate shaping of foam for bespoke acoustics and other specialized applications.
- Water Jet Cutting: Uses high-pressure water to cut foam without damaging its structure.
- Die Cut Press: Creates uniform foam shapes ideal for mass production.
2. Moulding and Fabrication
- Injection Moulding: Creates complex foam shapes for various applications.
- Compression Moulding: Forms foam into specific designs using heat and pressure.
- Laminating: Combines multiple foam layers for enhanced durability and functionality.
Types of Foam Used in Conversion
Different industries require various foam materials, each with distinct properties. Some of the most commonly used foams include:
1. Polyurethane Foam
- Widely used in cushions, mattresses, and soundproofing.
- Offers flexibility, durability, and excellent shock absorption.
2. Polystyrene Foam
- Lightweight with great insulating properties.
- Commonly used in packaging, disposable containers, and thermal insulation.
3. Polyethylene Foam
- Moisture-resistant and highly durable.
- Ideal for packaging, padding, and protective applications.
Applications of Foam Conversion
Foam conversion plays a crucial role in various industries. Some of the most common applications include:
1. Acoustic Solutions and Soundproofing
Bespoke acoustics solutions are an essential part of foam conversion, offering superior sound absorption and noise reduction for various industries. Foam is used in:
- Recording Studios: Reducing echoes and improving sound quality.
- Automotive Interiors: Minimizing engine noise and improving passenger comfort.
- Machinery Enclosures: Preventing excessive noise from industrial equipment.
- Marine Applications: Reducing sound pollution on boats and yachts.
2. Packaging and Protection
Foam is widely used in custom packaging to protect fragile and high-value items during transportation. Features include:
- Shock absorption
- Moisture resistance
- Thermal insulation
3. Medical Applications
In the healthcare industry, foam conversion is used for:
- Orthopaedic cushions and supports
- Medical mattress toppers
- Prosthetic padding
4. Automotive Industry
Foam conversion is vital in the automotive sector, where it is used in:
- Headrests and armrests
- Soundproofing for engines and interiors
- Thermal insulation for vehicle components
5. HVAC Systems
Foam conversion plays a role in Heating, Ventilation, and Air Conditioning (HVAC) by providing:
- Thermal insulation for ducting systems
- Noise reduction in air conditioning units
Benefits of Foam Conversion
Foam conversion offers numerous benefits that make it an ideal solution for various applications:
1. Customization and Versatility
- Products can be tailored to meet specific design and functionality needs.
- Multiple foam types and cutting techniques allow for unique solutions.
2. Enhanced Durability and Performance
- Foam conversion improves the lifespan and efficiency of products.
- Laminating and coating techniques enhance strength and resilience.
3. Noise Reduction and Soundproofing
- Bespoke acoustics solutions help control noise levels in various industries.
- Effective in reducing echoes, vibrations, and external noise pollution.
4. Environmental Benefits
- Some foam materials are made from recycled and eco-friendly materials.
- Helps reduce waste by repurposing foam into useful applications.
Quality Control in Foam Conversion
Ensuring high-quality foam products is essential for customer satisfaction and industry standards. Key quality control measures include:
- Rigorous testing for durability, flexibility, and fire resistance.
- Compliance with industry regulations and safety standards.
- Use of advanced technology for precise cutting and moulding.
Read also: Fitted Bathrooms: Enhance Comfort and Functionality in Your Home
Conclusion
Foam conversion is a vital process in many industries, offering innovative and tailored solutions for acoustics, insulation, packaging, and medical applications. With advanced cutting techniques and high-quality materials, businesses can develop durable and effective foam products to meet their specific needs. Whether it’s for bespoke acoustics, soundproofing, or industrial applications, foam conversion remains an essential part of modern manufacturing.
For businesses looking to enhance their acoustic and insulation solutions, foam conversion provides endless possibilities. By leveraging the latest technology and materials, industries can create high-performance foam products that offer superior comfort, protection, and noise control.